Table of Contents
Introduction to AI in Warehouse Management
Picture this: a warehouse that not only forecasts demand accurately but also maximizes inventory amounts and delivers each order with precision, all while lowering operational expenses. That’s no longer far-fetched; it’s turning into reality through the contemporary power of artificial intelligence (AI) in warehouse management. Artificial intelligence (AI) is picking up pace in the age of Logistics 4.0, focusing on the digitalization of goods distribution processes.
As the market for global warehouse management systems draws near an estimated $30.73 billion in 2025 with a CAGR of 14.02%, companies realize they need to shift to keeping pace with changing consumer needs and increased competition. A warehouse equipped with AI maximizes the usage of technologies such as machine learning, robotics, and the Internet of Things (IoT) to automate procedures, reducing manual intervention in monotonous functions and increasing general efficiency.
By substituting manual procedures with automated systems that can receive, sort, pick, pack, and cycle count, AI warehouse management not only accelerates processes but also minimizes errors, which are expensive to supply chains. With this new wave of warehouse management, organizations are leveraging AI to develop smooth workflows that improve efficiency and customer satisfaction.
AI in warehouse management: How is it used?
Today’s warehouse operations increasingly depend on advanced solutions like stacker cranes and motorized shuttles to simplify processes. These technologies alleviate the drudgery of repetitive work, improve flexibility, and reduce physical exertion for employees. The outcome is an automated warehouse, or a smart warehouse, which uses robotics, machine learning, predictive analytics, and an AI-powered Warehouse Management System to perform time-consuming tasks. These traditionally tedious processes can be automated, allowing organizations to focus on strategic initiatives instead of getting bogged down in routine work.
Imagine a system that doesn’t just react to your current inventory levels but anticipates your needs based on historical data, trends, and seasonal variations. This level of foresight can significantly reduce stockouts, minimize excess inventory, and optimize warehouse space. In a world where speed and accuracy are paramount, leveraging AI to improve warehouse management is not just an advantage; it’s a necessity.
Key Features of a Warehouse Management System
1. Automated Inventory Management
For a system to perform well in warehouse management, it must provide real-time inventory level and location tracking. Detailed movement logging from goods received to goods shipped provides traceability and visibility.
Key features are:
- Real-time updates of inventory status
- Stock Keeping Unit (SKU) support
- Attribute logging for serial numbers, batches, and best-before dates
- Barcode scanning for precision
- Inventory allocation for orders and tasks (FIFO, FEFO)
- Movement reporting and stock-taking capabilities
2. Warehouse Location Management – Dynamic Slotting
Effective location control is essential to maximize warehouse space. Major features are:
- Distinctive location IDs by aisles, columns, and shelves
- Multiple warehouses or internal zones support
- Barcode scanning for increased inventory control
- Diverse location types (bulk, picking, etc.)
- Location traffic and content reporting
- A visual warehouse map for convenient navigation
- Access control for security and safety regulations
3. Goods In Processes
Effective management of incoming goods is critical. A WMS needs to offer visibility into future deliveries to enable efficient resource planning. Key functions are:
- Advanced shipment notices (ASN)
- Delivery schedules
- Serial Shipping Container Code (GS1) support
- Staged receipt and put-away operations
- Recommended put-away policy for optimal space utilization
4. Order Management
A contemporary warehouse needs to handle orders through different channels, such as online ordering and manual inputs. An effective WMS enables:
- Centralized management of orders
- Multi-channel receipt and order updates
- Backorder management and automation
- Order tracking and reporting
5. Shipping Management
Automation improves shipping efficiency. Major features are:
- Automated courier service selection
- Document generation and label creation
- Integration for tracking information
- Reporting and analytics to streamline shipping strategies
6. Order Picking and Packing
Efficient picking and packing adjust according to order quantity and product type. Major capabilities are:
- Support for multiple picking methods
- Barcode scanning for confirmation
- Walk sequencing to optimize efficiency
- Double confirmation processes
- Document generation for dispatch
7. Returns Management
A seamless returns process is critical for customer satisfaction. A WMS must offer:
- Return logging against orders or blind receipts
- Reason documentation and return actions
- Inspection processes for restock or scrapping
- Reporting features to analyze return trends
8. Integrations
Integrating a WMS with other systems adds functionality. Consider:
- Prebuilt integrations with common order sources and couriers
- Finance and CRM software connection options
- Open APIs for custom integration
- Integration error reporting capabilities
9. Mobile Functionality
With growing warehouse requirements, mobile access is crucial. Features to look for are:
- Mobile barcode scanning for warehouse operations
- Internet dropout protection
- Access to cloud-based systems through mobile devices
10. Reporting and Analytics
Real-time reporting and analytics inform decision-making. Important functions should include:
- Reports on inventory, stock movement, and order status
- Trend analysis for optimization and forecasting
- AI-based predictive analytics for resource planning
- Custom reporting capabilities and scheduled reports
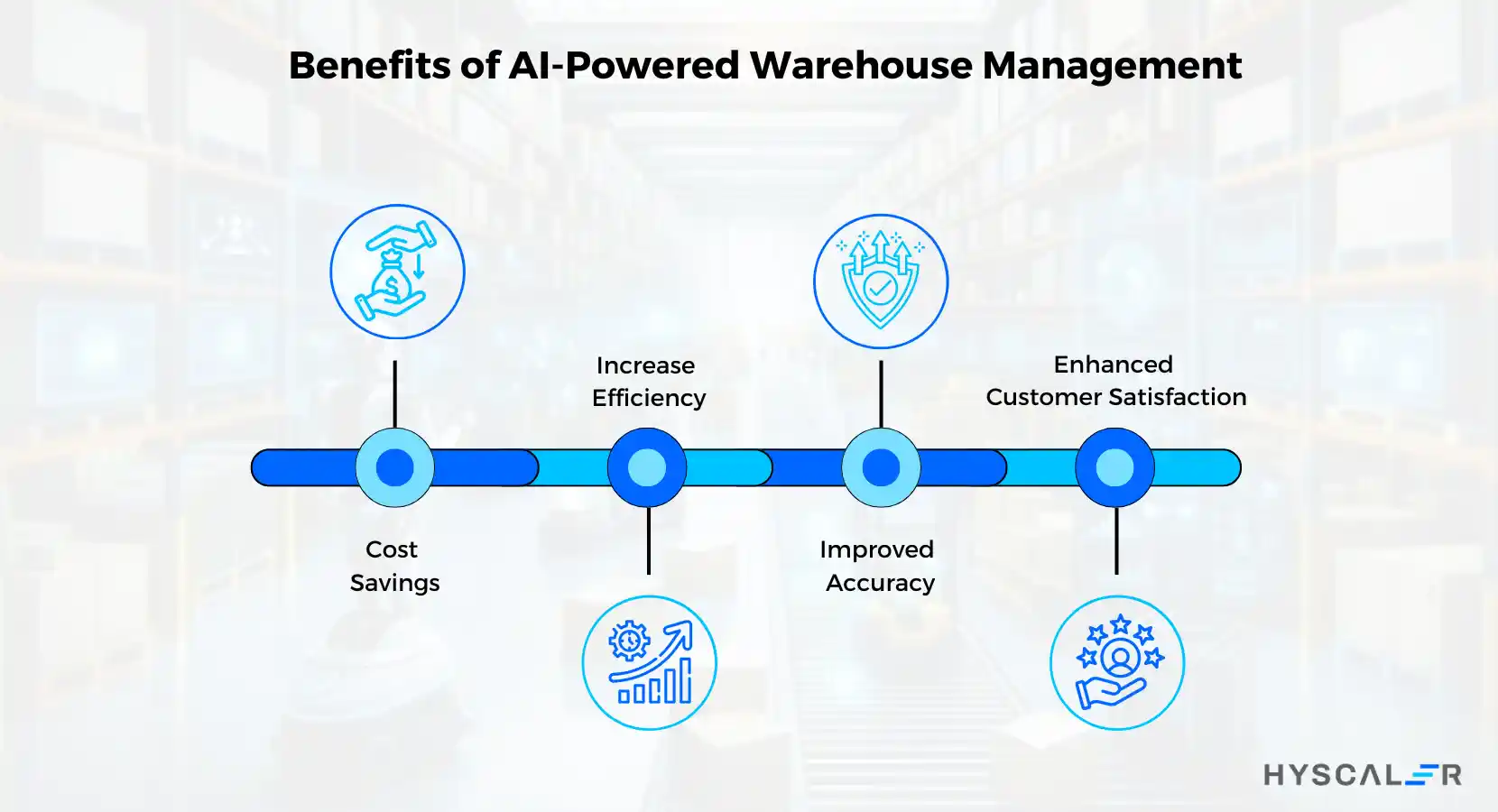
Real-World Implementations and Case Studies in Warehouse Management
Case Study 1: Amazon
Amazon makes extensive use of AI in warehouse management, utilizing robots to help with inventory work. The technology has cut the amount of walking done by employees by 40%, allowing Prime orders to be filled in hours, improving customer satisfaction greatly.
Case Study 2: XPO Logistics
XPO Logistics employs AI-based predictive analytics to improve its inventory management. Through the system, the company has eliminated 25% excess inventory and enhanced order lead times by 15%. Furthermore, the use of automated guided vehicles (AGVs) has improved picking efficiency by 30%.
Case Study 3: Walmart
Walmart relies on AI-driven demand forecast to simplify warehouse management. This anticipatory strategy helps the company keep inventory at the right level, which reduces waste by 10% and enhances inventory turnover rates, especially during holiday shopping seasons.
Designing an E-3PL System for Warehouse Automation
A startup in the U.S. created a cutting-edge warehouse management system (WMS) that automates vital logistics processes. With capabilities such as automated restocking and up-to-date inventory tracking, the system was an impressive 99.9% accurate on its orders, revealing the influence of technology on operating efficiency.
Installation of Predictive Analytics for Smart Inventory Management
A customer improved their old WMS by combining predictive analytics and achieved a cost savings of 15% in inventory. Machine Learning is used by the system to give actionable replenishment advice, allowing businesses to maximize inventory levels and react faster to customers’ needs.
Offering Warehouse Navigation to accelerate order picking
A German retailer improved order picking with a warehouse navigation mobile app, which produced optimized routes. This solution decreased picking time by 25%, showing how efficiently warehouse management software can improve productivity.
These case studies show the power of technology to transform warehouse management, revealing better efficiency, cost savings, and improved customer satisfaction.
Challenges of an AI-Powered Warehouse Management System
In spite of the many advantages of having an AI-based Warehouse Management System (WMS), there are a number of challenges that need to be tackled:
- Legacy Systems Integration: Firms usually encounter sophisticated and expensive integrations when trying to bridge new AI technology with legacy warehouse management systems.
- Staff Adjustment: It takes time and commitment to train employees in order to use new AI technology, posing a constant challenge to enterprises.
- Data Security: As AI systems continue to grow in prominence, data privacy and cybersecurity become more important, requiring active steps to safeguard sensitive data.
The Future of AI in Warehouse Management
The warehouse management future is in the full-scale deployment of AI technologies that increase speed, efficiency, and intelligence in operations. With advancements in data analytics and machine learning models, we can expect greater integration of AI into warehouse systems, unlocking new productivity levels.
Overall, AI-based warehouse management offers tremendous potential for businesses looking to refine their supply chain and improve efficiency. Those who invest in the technology will better be able to react to changes in the marketplace, eventually translating into better customer loyalty and satisfaction. For businesses exploring AI-driven efficiency, this co-warehousing guide highlights strategies to optimize shared warehouse spaces.
Take Your Warehouse Management to the Next Level
Welcome the future with HyScaler’s AI-Powered WMS. Simplify your operations, cut costs, and improve accuracy with cutting-edge features designed to meet your specific needs.
Find out how HyScaler can transform your warehouse management now!