Table of Contents
In the domain of precision engineering and quality control, Coordinate Measuring Machines (CMMs) have long been the cornerstone. However, the advent of Artificial Intelligence (AI) and Machine Learning (ML) is heralding a new era for CMMs, especially in retrofitting older systems. This article explores how AI and ML innovations, coupled with CMM Retrofit Software, are transforming CMM retrofit software, enhancing functionality and efficiency.
AI-Driven Data Analysis in High-Precision Industries
AI-driven data analysis, coupled with CMM Retrofit Software, leverages sophisticated algorithms to enhance the processing and interpretation of measurement data significantly. This advancement is particularly crucial in high-precision industries like aerospace, automotive manufacturing, and semiconductor fabrication, where accuracy is paramount.
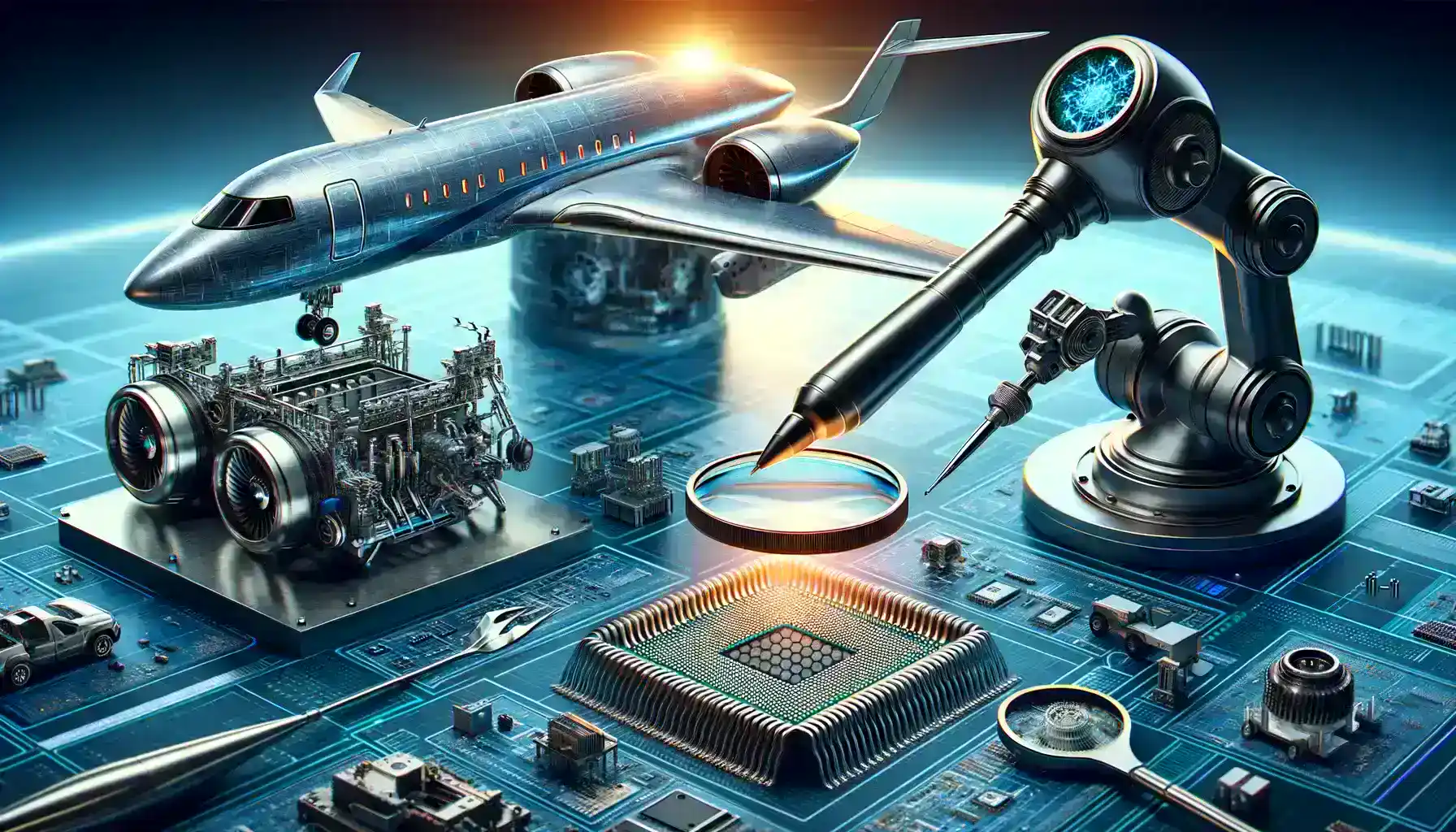
Aerospace Industry: In the aerospace sector, companies like Boeing and Airbus use AI-driven data analysis for inspecting aircraft components. These AI algorithms can quickly analyze data from CMMs, identifying even minute discrepancies in component dimensions that might affect aircraft performance and safety.
Automotive Manufacturing: Major automotive manufacturers like General Motors and Tesla have incorporated AI in their quality control processes. For instance, AI algorithms are used to analyze data from CMMs to ensure the precise assembly of critical components like engine parts, ensuring they meet stringent safety and performance standards.
Semiconductor Fabrication: In semiconductor manufacturing, companies like Intel and Samsung utilize AI for analyzing manometric measurements. This precise analysis is essential for ensuring the functionality of microchips, where even the smallest deviation can lead to significant performance issues.
Impact and Adoption by Companies:
AI-driven data analysis allows these companies to achieve a higher level of precision and reliability in measurements, translating into improved product quality and reliability.
It also enhances the efficiency of the measurement process, allowing for quicker decision-making and faster turnaround times in manufacturing.
Companies are increasingly adopting this technology due to its ability to handle large volumes of data and its superior accuracy compared to traditional methods.
Machine Learning for Error Compensation in Precision Measurement
Machine Learning algorithms, combined with CMM Retrofit Software, have become a game-changer in precision measurement by learning from historical measurement errors. This capability enables real-time adjustments and significantly enhances the accuracy of future measurements.
Precision Engineering Firms: Companies specializing in precision engineering, like Hexagon and Mitutoyo, use ML for error compensation in their measurement equipment. These algorithms analyze past measurement errors from CMMs, enabling the machines to adjust and compensate automatically for similar errors in future operations.
Impact and Adoption by Companies
By incorporating ML for error compensation, companies are able to reduce waste and rework caused by measurement inaccuracies.
This technology also enhances the overall reliability of the measurement process, which is crucial in industries where even minor errors can have significant consequences.
The ability of ML algorithms to adapt and learn continuously results in a consistent improvement in measurement accuracy over time.
Automated Feature Recognition in Coordinate Measuring Machines
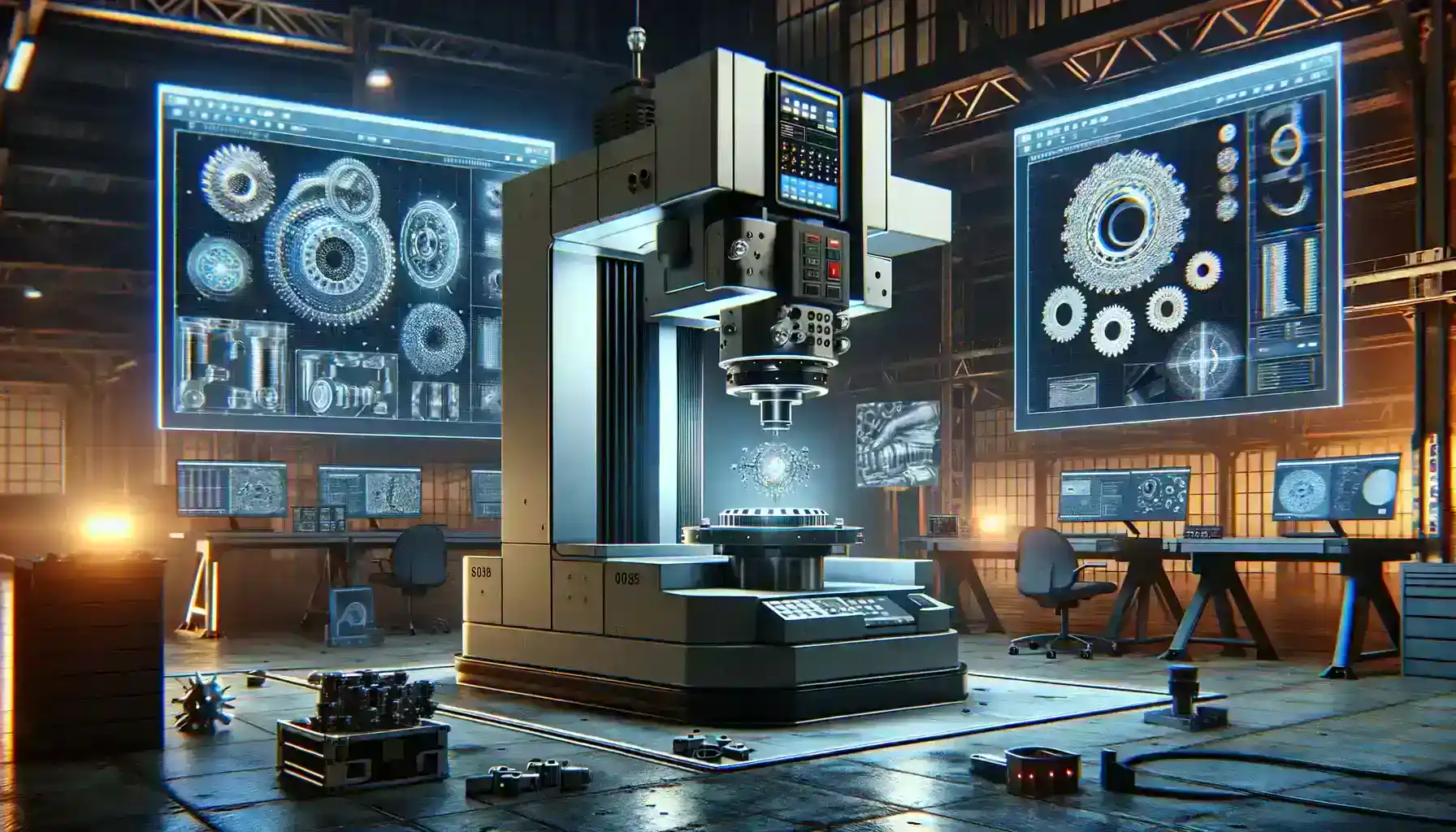
Automated Feature Recognition (AFR), coupled with CMM Retrofit Software and powered by AI, is transforming the use of Coordinate Measuring Machines (CMMs) in various industries. This technology enables CMMs to automatically identify and measure complex geometries, significantly reducing the need for manual programming and intervention.
Tool and Die Manufacturing: Companies in tool and die manufacturing, such as Kennametal utilize AI-driven AFR in their CMMs. This technology allows for the automatic recognition and measurement of complex tool geometries, streamlining the quality assurance process and ensuring high precision in tool production.
Automotive Parts Manufacturing: In the automotive sector, companies like Bosch are adopting AI-enabled CMMs for parts inspection. AFR technology allows these CMMs to quickly and accurately identify and measure various parts, from engine components to intricate transmission systems, reducing inspection times and enhancing accuracy.
Aerospace Component Inspection: Aerospace manufacturers, including Boeing and Northrop Grumman, use AFR in their CMMs for inspecting complex aerospace components. The AI-driven feature recognition enables quick and precise measurement of intricate parts, ensuring they meet the stringent quality standards of the aerospace industry.
Impact and Adoption by Companies:
AFR technology significantly reduces the time and labor involved in programming CMMs for complex part measurements.
It minimizes human errors associated with manual programming, leading to more consistent and reliable measurements.
The technology enhances the efficiency of the inspection process, allowing for quicker turnaround times in production cycles.
Predictive Maintenance Using AI in Coordinate Measuring Machines
Predictive Maintenance powered by AI algorithms, in conjunction with CMM Retrofit Software, has become increasingly important in the maintenance of Coordinate Measuring Machines (CMMs). By predicting potential machine failures, this technology, along with CMM Retrofit Software, ensures timely maintenance, thereby reducing downtime and extending the lifespan of the equipment.
Manufacturing Industry: Leading manufacturing companies like Siemens and General Electric are leveraging AI-driven predictive maintenance for their CMMs and other critical machinery. These AI algorithms analyze operational data to predict when a machine component might fail, allowing for maintenance to be scheduled proactively before a breakdown occurs.
Automotive Sector: Automotive companies such as Toyota have incorporated predictive maintenance in their production lines. For their CMMs, AI algorithms monitor various parameters like vibration, temperature, and operational patterns to identify signs of wear or potential failures, ensuring maintenance is done before the machines malfunction.
Heavy Machinery and Equipment: Companies like Caterpillar and John Deere, known for heavy machinery, use AI-based predictive maintenance to monitor the health of their CMMs. By predicting maintenance needs, they can avoid unexpected equipment downtime, which is crucial in high-stakes environments like construction and agriculture.
Impact and Adoption by Companies:
Predictive maintenance minimizes unplanned downtimes, which are costly and disruptive, especially in industries where production timelines are critical.
It leads to more efficient use of maintenance resources, as servicing is done based on actual machine conditions rather than on a fixed schedule.
This proactive approach to maintenance extends the overall lifespan of the CMMs, ensuring a better return on investment for the companies.
Integration of AI-Enhanced CMM Retrofit Software in Smart Manufacturing
The integration of AI-enhanced CMM retrofit software into smart manufacturing systems represents a significant step forward in industrial automation. This integration ensures a cohesive and efficient quality control process, leveraging the interconnectedness and intelligence of modern manufacturing environments.
Electronics Manufacturing: Major electronics manufacturers, such as Foxconn, utilize AI-integrated CMMs in their smart factories. These systems are connected with assembly line robots and other automated inspection equipment, ensuring high precision in the manufacturing of complex electronic components and devices.
Impact and Adoption by Companies:
The integration of AI-enhanced CMMs into smart manufacturing systems results in a significant increase in production efficiency and product quality.
It enables real-time data sharing and decision-making, allowing for immediate adjustments in the manufacturing process to maintain quality standards.
Customization and Flexibility in AI-Enhanced CMM Retrofit Software
The advent of AI in CMM retrofit software has introduced unprecedented levels of customization and flexibility, making these systems adaptable for a wide range of CMM types and measurement tasks.
Diverse Manufacturing Environments: Companies like Renishaw offer AI-enhanced CMM retrofit software that can be customized to fit various types of CMMs, whether they are bridge, gantry, or horizontal arm types. This flexibility allows manufacturers, regardless of their existing CMM hardware, to upgrade their measurement capabilities without needing to invest in entirely new systems.
Small and Medium-Sized Enterprises (SMEs): SMEs in sectors like precision tooling and fabrication, such as SME Precision and ToolCraft, benefit from the adaptability of AI-driven CMM software. This technology enables them to perform complex measurements that were previously only feasible for larger companies with more resources.
Impact and Adoption by Companies:
The ability to retrofit existing CMMs with AI software means companies can extend the life and functionality of their current measurement equipment, making it a cost-effective solution.
AI-driven customization allows for quicker setup times for new measurement tasks, enhancing overall productivity.
This flexibility is especially beneficial for companies that deal with a variety of products or those that need to frequently change their production lines.
Enhancing User Experience and Training in CMM Operations with AI
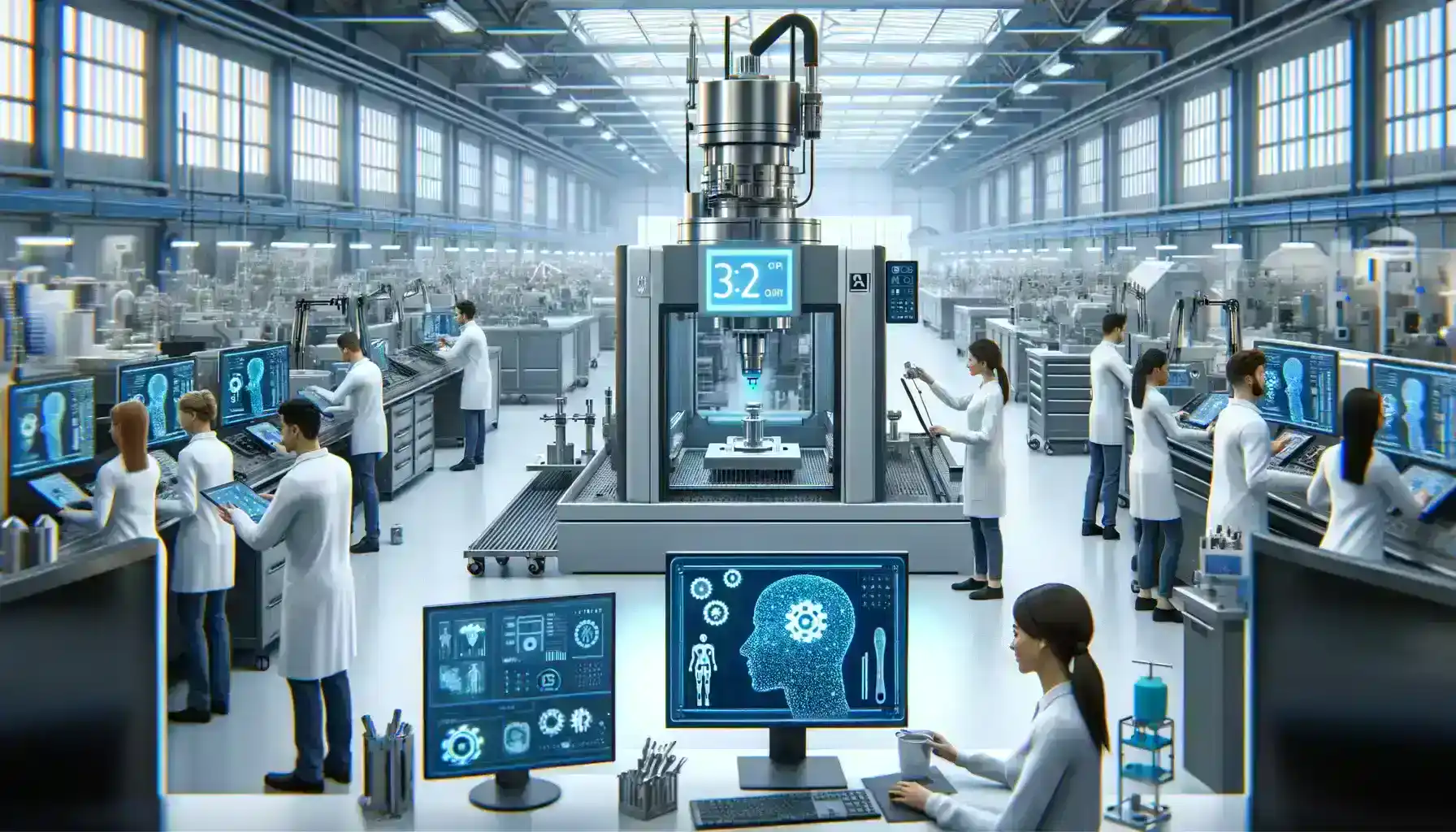
The integration of AI in CMM software has greatly simplified user interfaces, making these systems more user-friendly and reducing the learning curve for operators. This advancement is particularly significant in industries where precision and ease of use are paramount.
Medical Device Manufacturing: Companies like Medtronic which manufactures precision medical devices, benefit from the simplified operation of AI-integrated CMM retrofit software. The intuitive interface allows operators to quickly learn and accurately perform intricate measurements required in medical device manufacturing.
Impact and Adoption by Companies:
AI-driven user interfaces in CMM retrofit software lead to a significant reduction in the time and resources needed for operator training.
Simplified interfaces increase the accessibility of CMMs, allowing a broader range of employees to operate them, which is particularly beneficial for companies with a high turnover rate or those expanding their workforce.
Enhanced usability also reduces the likelihood of human error in measurements, contributing to improved overall quality and precision in manufacturing processes.
Conclusion
The integration of AI and ML into CMM retrofit software is not just a futuristic concept; it’s a current reality that’s reshaping the landscape of precision measurement. While there are challenges, such as cost and complexity of integration, the advantages like increased accuracy, efficiency, and predictive maintenance capabilities make a compelling case for adoption. As we move forward, these technologies will continue to revolutionize the field, setting new standards for precision and efficiency in manufacturing and quality control.