Table of Contents
In the automotive industry, repair order management plays a critical role in ensuring efficient workflow, proper documentation, and excellent automotive service. Automotive Repair Order Management involves tracking all tasks related to vehicle repairs, from the initial customer request to job completion, including documentation, parts ordering, labor allocation, and invoicing. A well-managed repair order system helps repair shops stay organized, minimize delays, and optimize resource use.
This article will explore 10 best practices for effective Automotive Repair Order Management, improving overall efficiency and customer satisfaction.
What is Automotive Repair Order Management?
Automotive Repair Order Management refers to the process of organizing, tracking, and managing all aspects of vehicle repair jobs from start to finish. This includes creating repair orders, assigning technicians, tracking labor and parts used, invoicing, and ensuring that all tasks are completed accurately and efficiently.
By implementing a structured system, repair shops can streamline their workflow, reduce delays, and enhance customer satisfaction. In essence, it helps keep repair processes transparent, organized, and efficient.
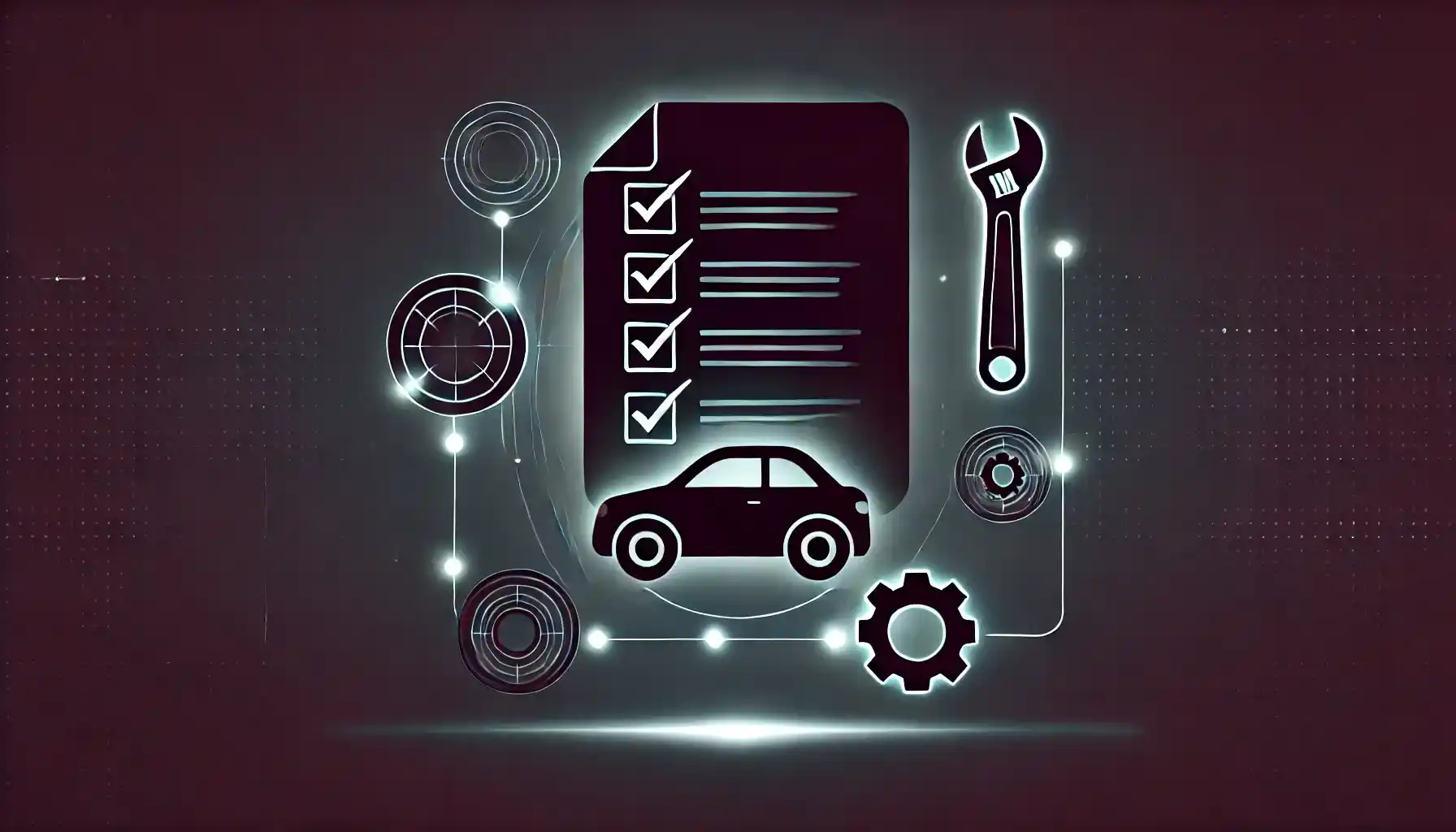
1. Use a Digital Management System
One of the most impactful ways to improve repair order management is by implementing a digital system. Paper-based repair orders can easily get misplaced, damaged, or lead to miscommunication. A digital Automotive Repair Order Management system helps track repair statuses, assign technicians, and store data centrally.
Additionally, it enables real-time updates, which increases transparency between the repair team and customers. Look for software that integrates with inventory, billing, and scheduling systems to streamline operations.
2. Ensure Accurate Initial Diagnosis
A common cause of delays and inefficiencies in repair shops is inaccurate diagnostics at the start of the process. Providing a precise estimate of the issues, parts required, and expected completion time is crucial. The more accurate the initial assessment, the easier it is to manage the entire repair process.
Train technicians to be thorough when diagnosing issues and documenting them in the system, avoiding miscommunication and the need for repeat work.
3. Automate Scheduling and Labor Allocation
Properly scheduling work orders and assigning technicians is essential to avoid bottlenecks in the repair shop. An efficient way to achieve this is by automating scheduling and labor assignments based on technician availability, skillset, and workload.
Modern repair order management systems allow to automate these processes, ensuring the right technician is assigned to each task, and preventing overbooking. This leads to faster turnaround times and better resource allocation.
4. Maintain an Organized Inventory
An effective Automotive Repair Order Management system should integrate seamlessly with inventory management to ensure that the necessary parts are always available. Parts delays are a frequent cause of repair hold-ups.
Keeping the inventory organized, with real-time updates, helps to stay ahead of demand, reduce downtime, and avoid unnecessary delays. This not only improves repair efficiency but also enhances customer satisfaction as repairs are completed on time.
5. Use Standardized Work Order Forms
Consistency is key when it comes to managing repair orders. By using standardized work order forms, technicians and service advisors can ensure that all essential information is captured for every repair job.
These forms should include fields for customer information, vehicle details, repair descriptions, parts used, labor time, and costs. Standardizing these forms reduces the chances of missed details, ensuring accuracy in communication and billing.
6. Communicate Clearly with Customers
Good customer communication is vital for the success of any repair business. Keep customers informed about their vehicle’s status, unexpected delays, or additional repairs needed.
This is especially easy with digital repair order management systems that offer real-time updates via text or email. Clear communication helps manage customer expectations and builds trust, ensuring repeat business and positive reviews.
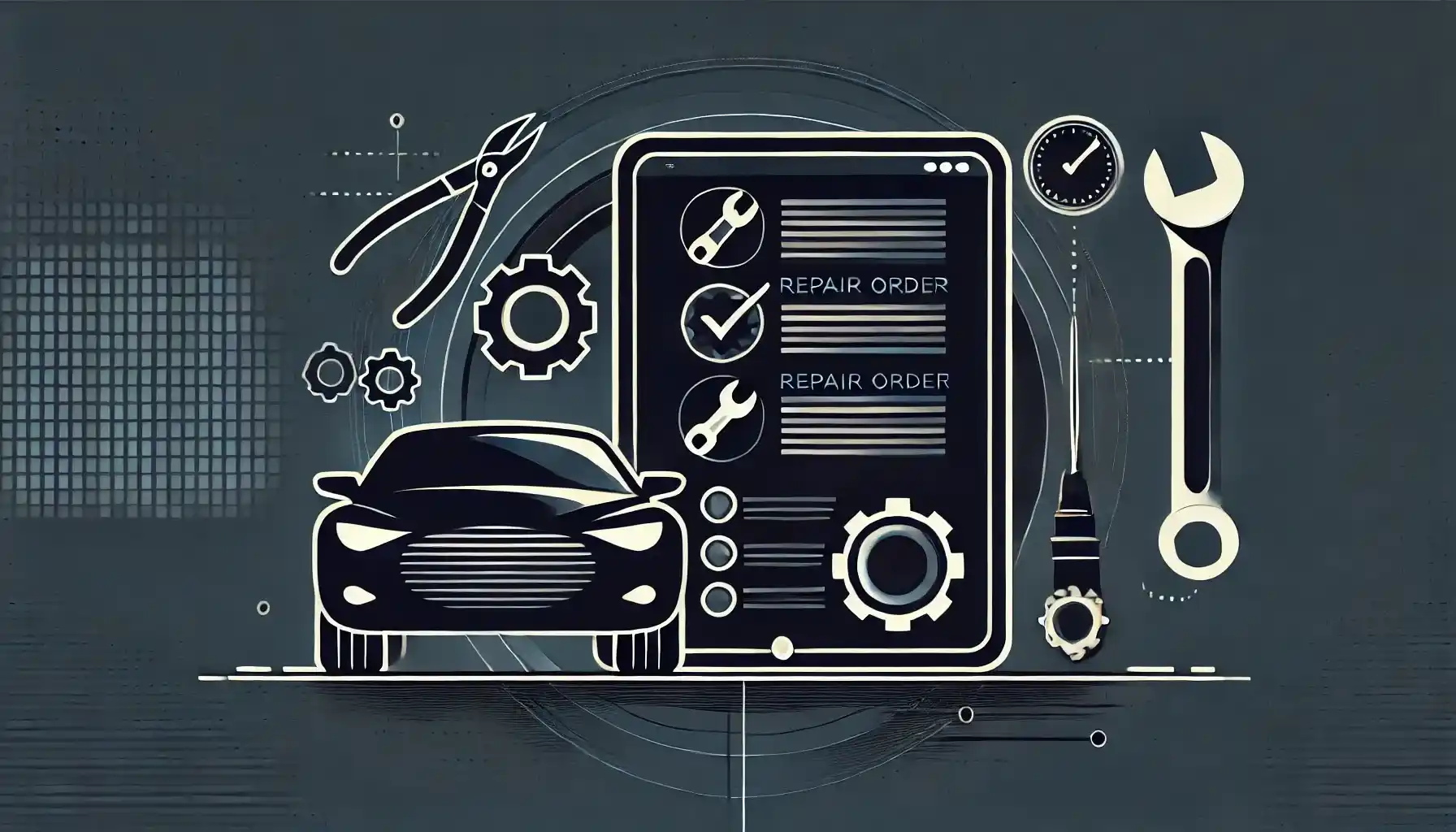
7. Regularly Review and Optimize Workflow
Automotive Repair Order Management isn’t a one-size-fits-all process. Regularly reviewing and optimizing the workflow ensures that it adapts to changes in demand, staffing, and shop capacity. Analyze data from the management system to identify bottlenecks and inefficiencies. Continuous improvement is key to long-term success.
Look for ways to streamline processes and make them more efficient, whether it’s upgrading equipment, adding new technology, or refining how repairs are documented.
8. Implement Quality Control Checkpoints
Maintaining high standards of repair work is essential for a successful shop. Introduce quality control checkpoints at critical stages of the repair process. Before a vehicle is handed over to the customer, conduct a final inspection to ensure all repairs have been done correctly, the vehicle is roadworthy, and no additional issues were introduced during the repair.
Incorporating quality checks into the repair order management process reduces the chances of comebacks and ensures customer satisfaction.
9. Track Key Performance Indicators (KPIs)
Tracking KPIs is essential to understanding how well the automotive repair order management is working. Common KPIs include repair turnaround time, technician efficiency, customer satisfaction, and parts availability.
By monitoring these metrics regularly, one can identify areas for improvement, adjust workloads, and optimize operations. This data-driven approach ensures it stays on top of shop performance and meets the business goals.
10. Offer Transparent Billing and Payment Options
Billing transparency is crucial for customer satisfaction. Ensure the automotive repair order management system offers detailed invoicing that breaks down parts, labor, and other fees. Customers appreciate clear, easy-to-understand bills, reducing the likelihood of disputes.
Additionally, offering multiple payment options, such as credit cards, mobile payments, or installment plans, provides flexibility and convenience, encouraging timely payment and customer loyalty.
Conclusion
Effective Automotive Repair Order Management is critical for the success of any repair shop. By following these 10 best practices—ranging from adopting digital solutions to maintaining an organized inventory and ensuring clear customer communication—one can optimize operations, reduce errors, and enhance customer satisfaction.
Remember that the key to long-term success is continuous improvement, so regularly review processes and adapt to evolving demands and technologies. Implementing these practices can help repair shops stay competitive and grow in an increasingly digital and customer-centric industry.